Classification and marking of bronze
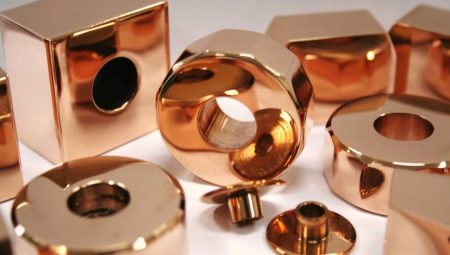
Bronze should be understood as a metal alloy based on copper, and alloying components are added to it, increasing the hardness of the finished material. Tin, chromium, lead, nickel, aluminum and other metals are most often used in the form of a ligature. The physical properties of the bronze alloy, as well as its color and hardness, will have different characteristics, which depend on the percentage composition of the alloy components.
Bronze, which has a pronounced red tint, consists of an increased amount of copper, and if the alloy has a grayish tint of steel, then the copper content in it is reduced to 30-35%. Bronze is a popular material that is used in various economic and industrial fields.
Peculiarities
Bronze alloy consists of copper and ligature, which can be both in the form of metals and non-metals - the grade of bronze depends on this composition. Through technological experiments and scientific research, the optimal relationship between the bronze base and its components has been found. The most commonly used additives are:
- beryllium;
- aluminum;
- zinc;
- tin;
- silicon;
- phosphorus;
- iron;
- manganese;
- lead;
- nickel.
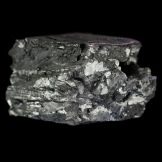
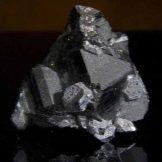
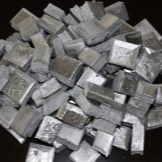
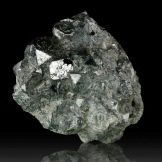
According to historical evidence, the first bronze material was created 3000 years ago and consisted of copper and tin... In small proportions, tin gives the remelted substance hardness, flexibility and facilitates the melting process itself. Tin exhibits such properties if its concentration in the material does not exceed 4-4.8%. If we take about 5% or more of tin, the finished alloy will lose its flexibility, and at a tin concentration of more than 20%, the resulting material will be brittle.If beryllium is added to the remelting to copper, then the output will be a solid material with increased physical and chemical resistance.
Products made from this metal alloy can be cut or welded using any kind of welding.
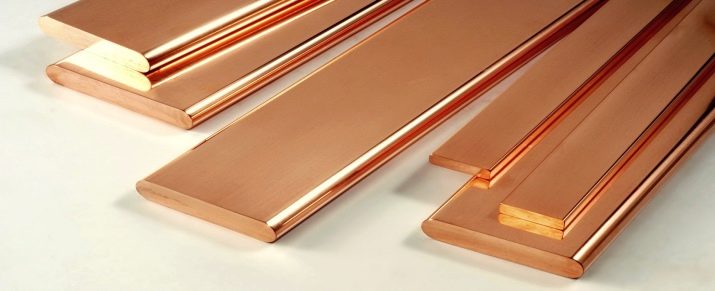
When copper is combined with silicon and zinc the finished material will have good plasticity, which is perfect for casting products. The finished product has increased wear resistance and does not spark during machining. In addition, bronze with silicon and zinc ligatures has a high level of resistance to thermal compression of the metal.
If you add lead to copper, you get a metal that has anti-corrosive qualities, slip and friction resistant, strong and difficult to melt.
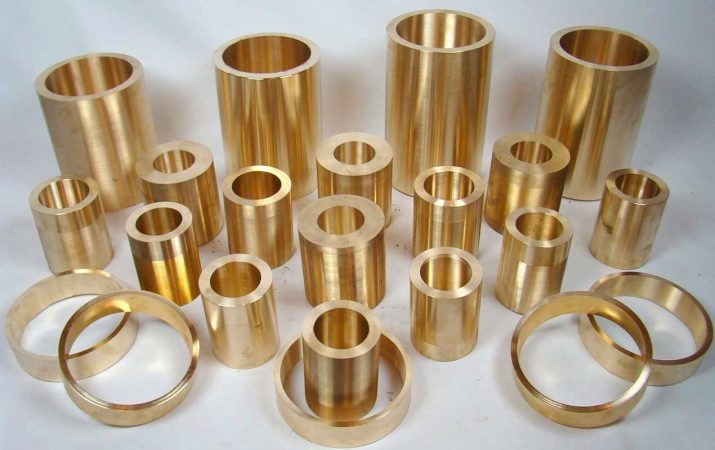
Combining copper with aluminum, You can get a material that will have a high density, reduced slip index, increased resistance to rust formation and resistance to aggressive chemical environments. This metal is suitable for cutting. If phosphorus is added to copper, then in conjunction with some other compositions of the master alloy, this ingredient will reduce the acidic properties of the alloy.
When any kind of ligature is added to copper, its ability to conduct heat is greatly impaired. The more ligature in the alloy, the worse its thermal conductivity level.
As for the appearance of the bronze alloy, with a content of up to 90% copper in it, the metal will have a red tint, and with a copper content of up to 85%, the material will have a yellow tint.
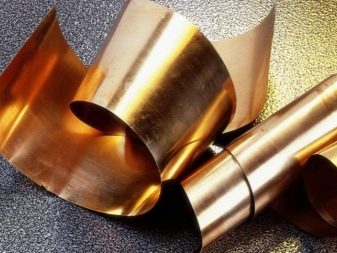
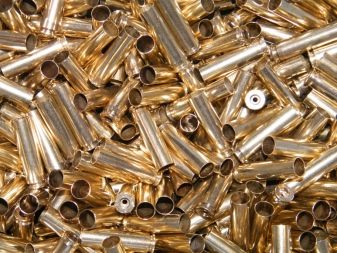
It is noticed that if the alloy consists of only 50% copper, then the material from it will be white steel in color, and in order to obtain a black color, the concentration of copper is reduced to 35%. Over time, all copper materials change their color: it darkens under the influence of temperature extremes, acids, salts, alkalis of various concentrations.
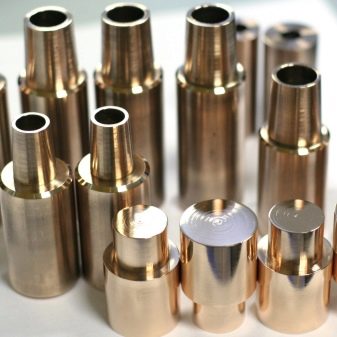
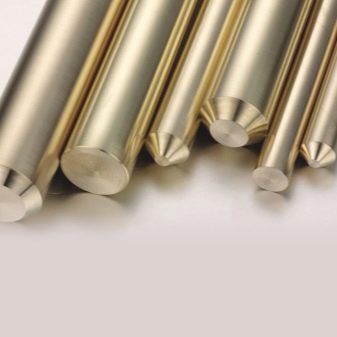
Basic classification of alloys
In accordance with how many components are included in the composition of the bronze alloy, bronze is conventionally subdivided into two-component (metal and ligature, consisting of 1 component) or multicomponent. In addition, bronze materials are divided into tinless and tin compositions. Tinless formulations do not contain tin. Their classification is made taking into account what kind of metal, instead of tin, performs the function of a ligature.
Pewter
By adding tin to copper, you can get casting alloy. But, in addition to a high fusibility index, this composition also has good hardness. Often, zinc, lead and phosphorus are also added to such a metal. This ligature imparts corrosion resistance to the finished material and makes it even more suitable for smelting and foundry work.
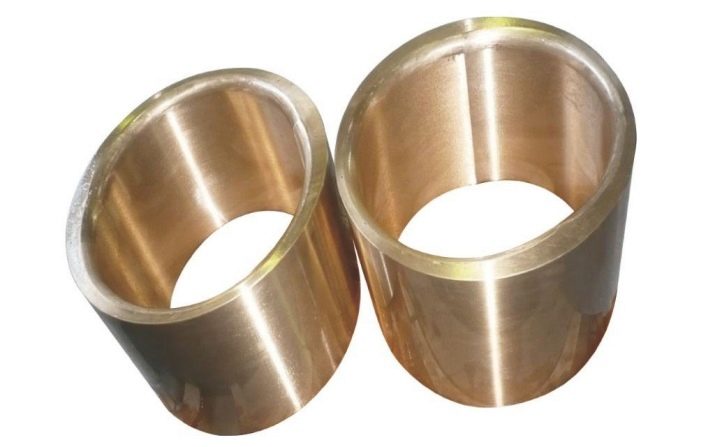
In tin alloy phosphorus acts as a metal deoxidizer, and zinc reduces the cost of the material due to its low price, and it does not have a special effect on the characteristics of the resulting metal. In order to save money, it is allowed to include up to 10% zinc in tin alloys. Tinned bronze grades are suitable for machining and polishing applications. Finished products made from pewter grades will be very durable.
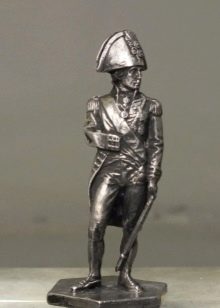
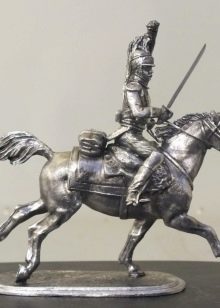
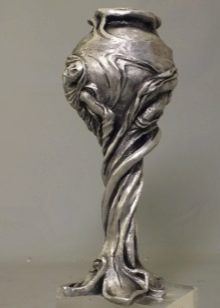
Bronze alloy, which contains up to 8% tin impurity, is used for stamping, rolling and forging. Wire, rods of various shapes, as well as sheet metal are made of this material. Alloy, where tin takes up to 20% in the form of a master alloy, is used for the manufacture of cast products... In the casting process, such bronze completely fills the mold and has a small proportion of shrinkage. This material allows the production of complex shapes, as well as items of artistic significance.
In addition, tin bronze is used for the manufacture of units and mechanisms that will operate in seawater.
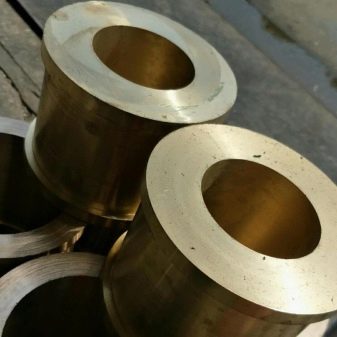
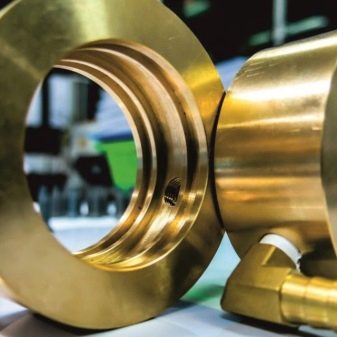
Aluminum
Aluminum is often used in bronze alloys. The ligature contains from 6 to 12% of such material. Bronze aluminum alloys can consist of one component (aluminum) or many additives, when iron, nickel and manganese are also present in the alloy. The addition of aluminum to bronze reduces the density of the finished material, so the lightweight alloy is widely used in shipbuilding and the aerospace industry.
The material with the addition of aluminum has a high frictional strength, therefore, the alloy is also used for the manufacture of parts for machine tools, heating equipment units, and road vehicles.
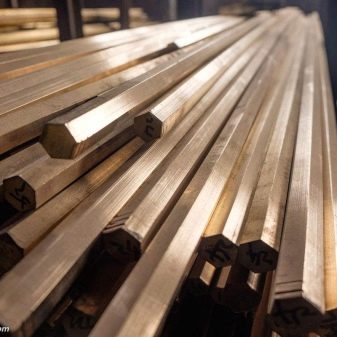
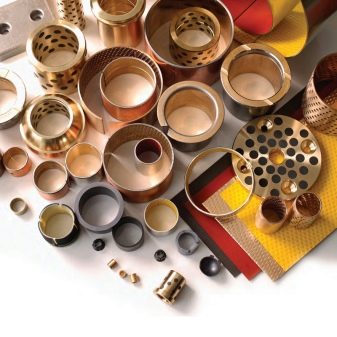
Siliceous
Silicon can be added to bronze in a proportion of 3 to 5%. The finished alloy is superior in its anti-corrosion properties to tin alloys, and also has high mechanical stability and elasticity. In addition, silicon alloys are not magnetized and are well suited for electric welding and soldering.
Finished copper with silicon products have high resistance to aggressive chemical environments in the form of acids and alkalis, as well as gases. Such material is used for the manufacture of gas mains or water drainage system.
Silicon bronze can be additionally alloyed with manganese.
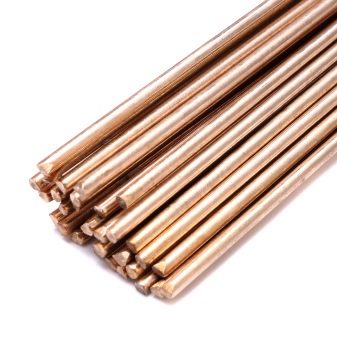
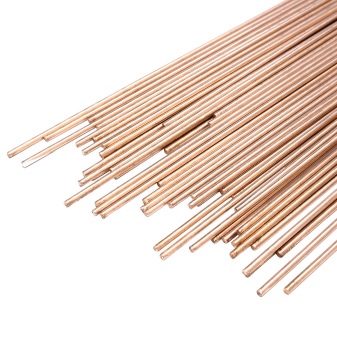
Manganese
In various spheres of industry it is in demand bronze alloy containing manganese: from 4 to 5%. The material has characteristic features: high strength, flexibility and anti-corrosion resistance. Parts for various mechanisms are made from such alloys. When the content of manganese in the bronze alloy is more than 1%, the hardness of the material increases, but the toughness and fusibility of the substance decreases.
In addition, manganese alloys are difficult to weld.
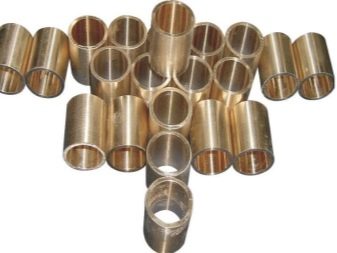
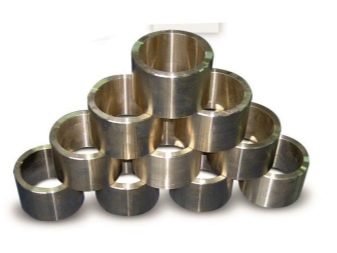
Lead
When a lead component is added to copper, a high-strength, abrasion-resistant alloy is obtained. It is used in the manufacture of bearings that rotate for a long time, under high pressure and at high speed. Bronze with a lead ligature is used for the manufacture of parts of devices operating in aggressive chemical environments, the material is used to protect against radiation, in the manufacture of ammunition, glass, as various coloring pigments for printing ink.
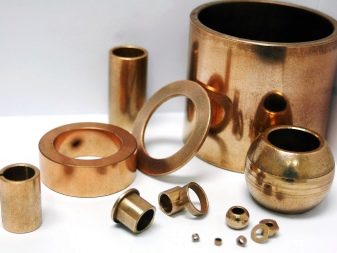
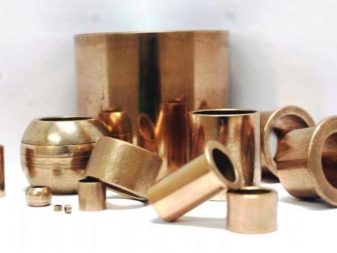
Beryllium
Adding beryllium to copper forms a bronze alloy, which is characterized by increased strength, flexibility and flow characteristics. In addition, the material possesses good electrical conductivity and is a heat conductor... The alloy is resistant to corrosion, products in the form of springs and complex mechanisms are produced from it, the material is used in electrical engineering in the manufacture of fiber-optic products and microcircuits.
Bronze alloy with beryllium allows you to make the smallest details from it, which can be used in instrumentation, computer and telephone technology, multimedia devices and so on. The rate of beryllium content in the alloy ranges from 0.7 to 2.5%.
After a special heat treatment, the alloy is hardened, which gives it the properties of increased hardness.
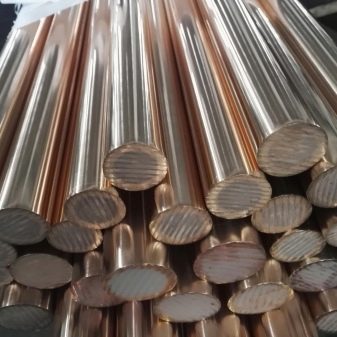
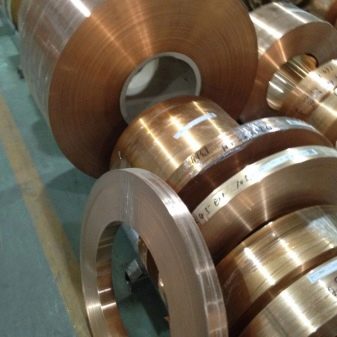
Marking
In order to distinguish bronze alloys from each other, a certain marking was introduced. And there are special tables for technical purposes, according to which the technologist can determine which brand of bronze to use for a particular task, to clarify the tabular data on the composition of the alloy, its physicochemical properties and possibilities of application.
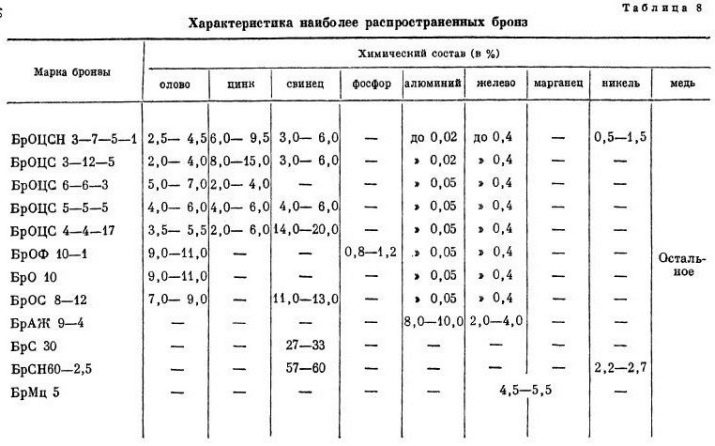
The existing brands of bronze differ from each other in the composition of the ligature as a percentage of copper. Bronze alloy marking has an alphabetic and numeric designation. For example, the decoding of such a mark may mean that the letters in the name will correspond to the chemical elements, and the numbers will indicate the percentage of the percentage of the ligature. According to GOST, digital data do not contain indications of the content of copper in the alloybecause it is clear that it is the main component.
But all ligature norms must comply with the established state standards.
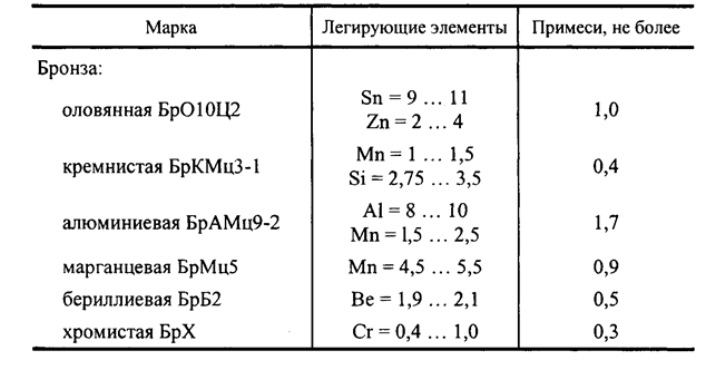
The bronze alloy is marked with the abbreviation Br. Next comes the letter indicating the main component of the ligature, and then the rest of the constituent parts. As for the numbers, they are arranged in descending order, indicating the percentage of ligature components. For example, bronze grade BRAZHN 10-4-5 is an alloy of copper with aluminum, iron and nickel. Moreover, aluminum in the composition of the alloy is 10%, iron - 4%, nickel - 5%. The rest is copper.
When the grade of the bronze alloy is unknown, the material is subject to chemical and physical analysis. Accurate data is needed for workers who need to determine the weight of the workpiece through the specific gravity of the alloy. Each steelmaking plant has its own technical laboratory, which helps to solve problems of this kind.
Bronze - what kind of metal and where is it used - see the video below.