All about bronze and brass casting
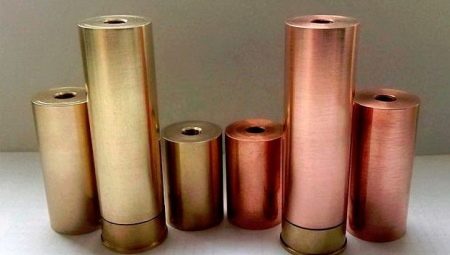
Bronze is an alloy of copper and tin, sometimes with the addition of silicon, aluminum and lead. It can have different colors, depending on the percentage of the components. There are several types of bronze:
- pewter;
- aluminum;
- lead.

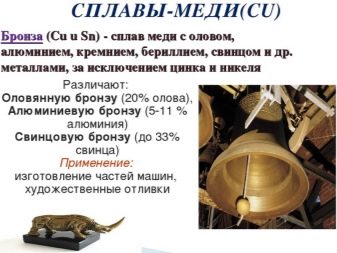
Tin bronze is the most widely used type and has low fluidity. It is convenient to cast products with specific dimensions from it. Since it does not need further processing. Brass is an alloy of copper with the addition of zinc. Usually the mixture is 70% copper, 30% zinc. Sometimes brass is found with a composition of 50 to 50.
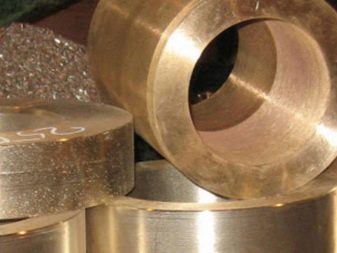
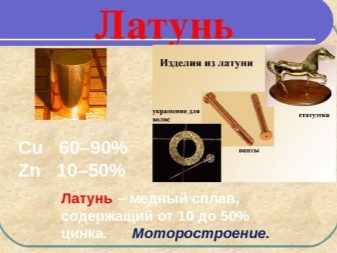
The advantages of bronze include the following.
- Practicality.
- Possibility to practice art casting at home.
- High resistance to environmental factors.
- Almost non-corrosive.
- Ease of processing.
- Durability.
- Electrical and thermal conductivity.
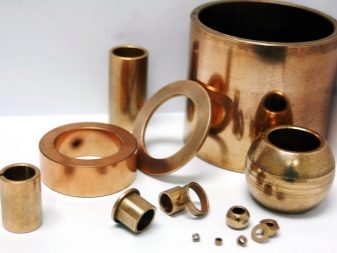
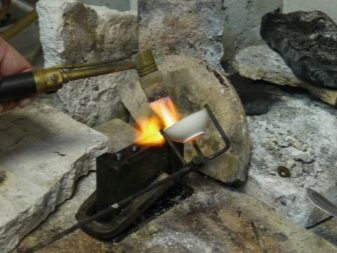
Brass is highly resistant to corrosion. It is used as a surface layer of other metals in the manufacture of metal structures.
History of technology
Casting brass, like bronze, appeared 12 thousand years ago. At first, tools and decorations were made from these materials, later dishes and household items. Items made of bronze and items made of brass were widely used in all spheres of life. The first methods of making bronze and brass originated in the ancient era in the era of classicism. We can contemplate many masterpieces of art of that era to this day. At the moment, these low-melting alloys are used mainly for the manufacture of decorative items for decoration and works of art.
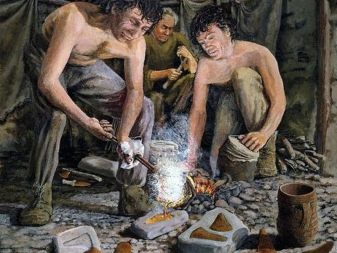
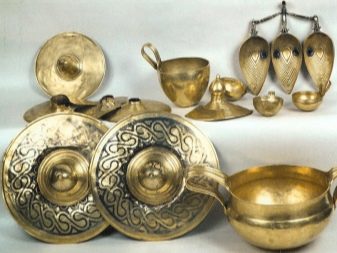
Copper alloys with the addition of metals are widely used in the production of:
- sculptures and souvenirs;
- gratings and other elements of fences;
- fences and gates;
- interior details;
- in the decoration of chandeliers and sconces.
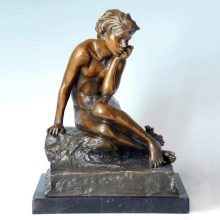
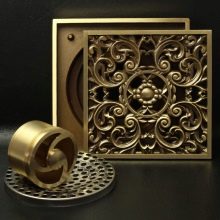
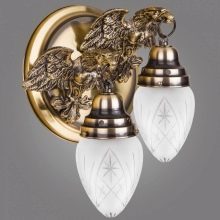
Over time, the injection method has been improved. And in the modern world it has become possible to smelt bronze and brass parts not only in an industrial way, but also in domestic conditions.
Peculiarities
Artistic brass casting is almost the same technology as bronze casting. Here are the subtleties of the process.
- The melting temperature of brass is rather low, in the range of 880-965 C. This allows different types of ovens to be used. Even a gas burner, it is enough to choose a heat-resistant cookware. But sometimes the temperature rises to 1070 C due to additives (for multicomponent brass). The melting point of bronze is higher. The alloy has copper with tin 900-950 C, and bronze without tin has 950-1100 C. Bronze alloys have a high toughness, therefore, to improve their quality, they are heated 100 higher. To save energy, it is better to use induction or crucible furnaces.
- The main stage of casting is pouring the melt into the mold. The duration of the process should not exceed 2 minutes. Otherwise, the product will be defective. Splits, burns and seams will appear. The thing will be completely damaged and unusable. Or additional processing will be required.
- For brass, there should be uniform gradual cooling, without the use of special solutions. When cooling bronze, coolants are used.
- The final stage is the processing of the finished part.... It is required to remove bays, sprues, risers. To keep the composition unchanged, fluxes are added to the alloy. Thanks to them, it is possible to protect the surface of the melt and degass its composition. This reduces waste on the finished product.
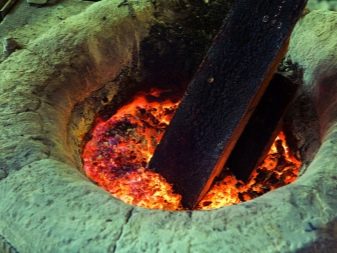
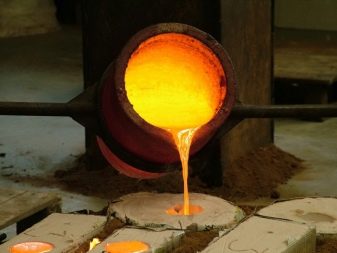
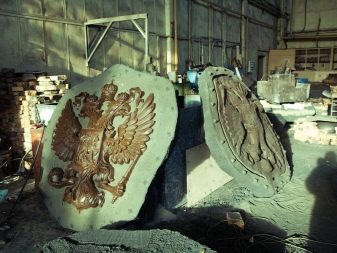
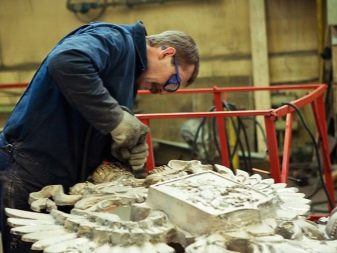
Necessary equipment
Here is a list of the main equipment for making figures from these materials.
- Casting shape. Made from various materials.
- Forcepsto remove the finished part from the mold.
- Crucible for melting the charge in it. The material of its creation is graphite and clay.
- Heating equipment, ovens... A gas burner and a heat-resistant container can be used to melt the brass.
- Various auxiliary materials: coal, forge
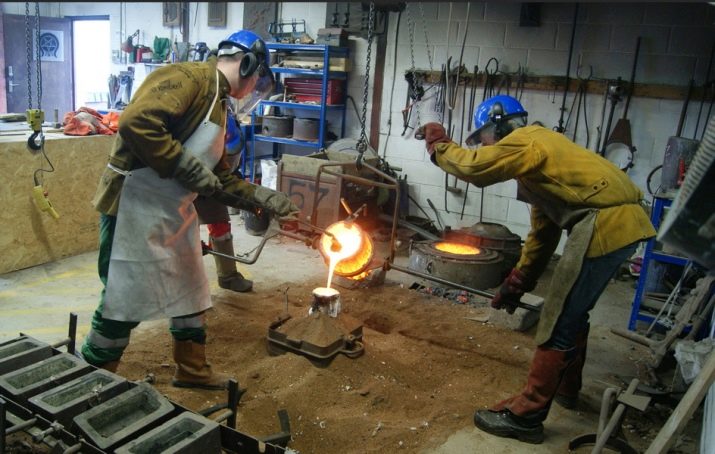
It is necessary to use a strict sequence of technology. First, place the crucible on the furnace, then put metal pieces into it. When fully melted, the mixture changes color. Then, using special equipment - a crucible is taken out of the furnace with a crochet hook and the melt is carefully poured into a casting mold. After complete cooling, the part is removed using forceps and subjected to final processing.
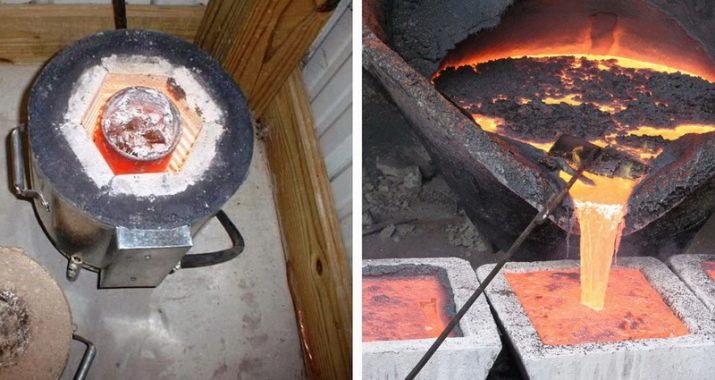
Casting models overview
Before you start casting the finished product, you must first create a sketch of the future shape. The drawing is carried out by special master artists. Then a casting mold will be created along it, into which the main melt is poured. The creation of a casting mold is a rather laborious and responsible task. For this, special compositions for molding, tools and devices are used. The finished model plays a major role in the entire technological process. Its internal cavity should be an exact copy of the finished product using lost wax molds. A molten solution is poured into it, which subsequently, being inside, cools down and takes on its final form.
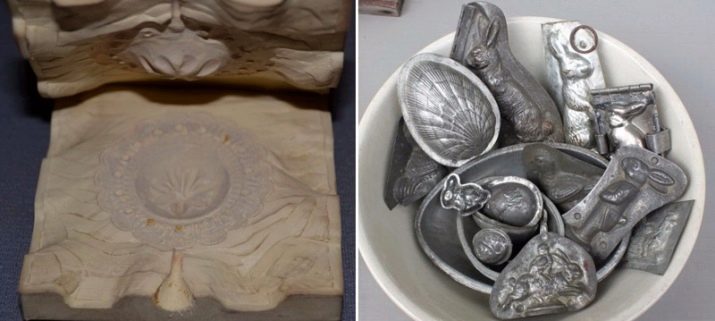
To give stability, so that during the ebb of the melt into the mold, it does not collapse, use flasks. It is a special device made of two rectangular connecting parts, similar to a box. Usually made of wood or plywood. In metal flasks, not only the creation of the casting mold takes place, but also the casting itself. Models for the manufacture of brass and bronze are reusable and disposable. It depends on what they are made of.
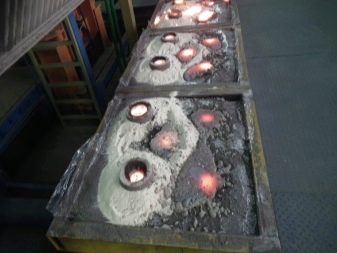
Materials (edit)
Ivory, wood, plaster and polymers. Steel is also used to make reusable molds. The least commonly used plastic material is used to create a casting model.At home, the melt is most often cast into a non-separable plaster mold. After the alloy has cooled and hardened into a finished figure, the shape is gently broken with a special hammer.
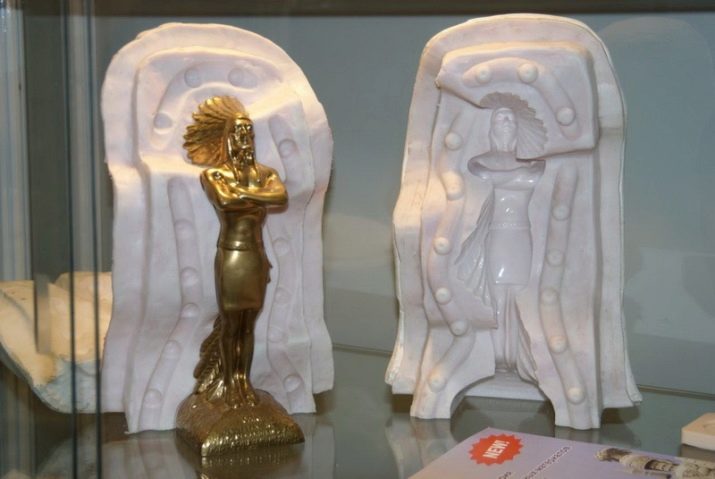
Constructions
Structurally, molds can be of three types.
- Detachable. This is a structure consisting of two or more parts, connected along a straight or complex surface. Disconnects to retrieve the finished product. Most often used in production for reusable use.
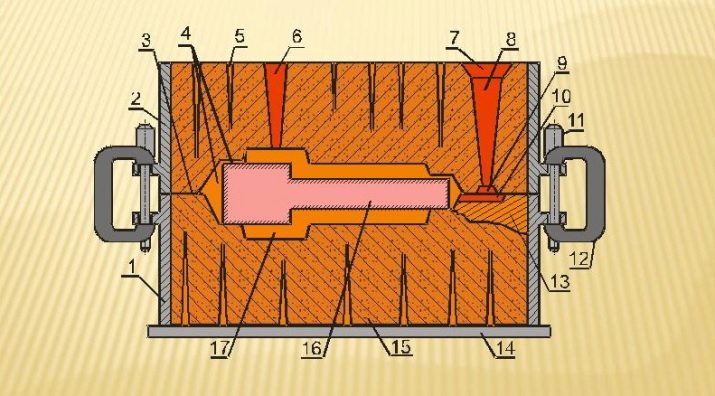
- One-piece... To extract the finished part, it is broken with a hammer. Suitable for single use only. It is made for a specific product according to sketches. It is often used in home production. Plaster is most suitable for creating such forms.
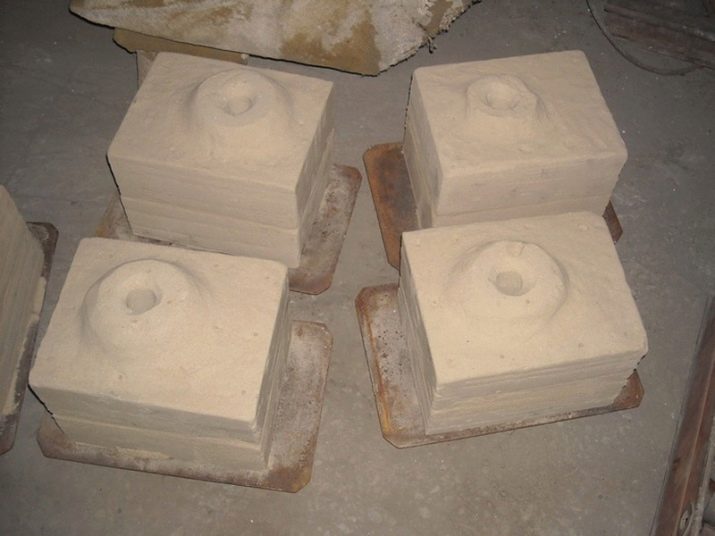
- Special... This is a complex mold or skeleton template. Differs in a large component. Created to melt complex shapes.
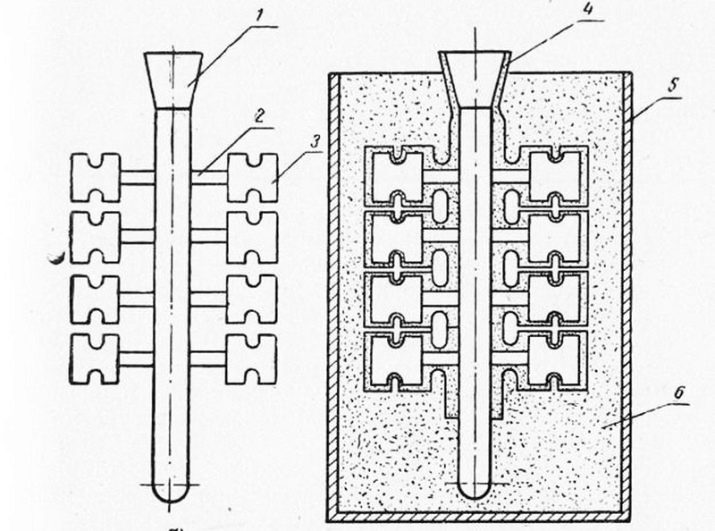
The main subtleties of casting
Centrifugal casting
This casting method is used to produce parts and equipment for mechanical engineering and other industrial sectors. The technology is based on centrifugal force. It appears due to the rotation of the casting model. This type of casting is used mainly for the manufacture of bodies of revolution. Forming can be carried out by vertical and horizontal casting machines. On machines with a horizontal axis of rotation, they make:
- liners;
- bushings;
- rings.
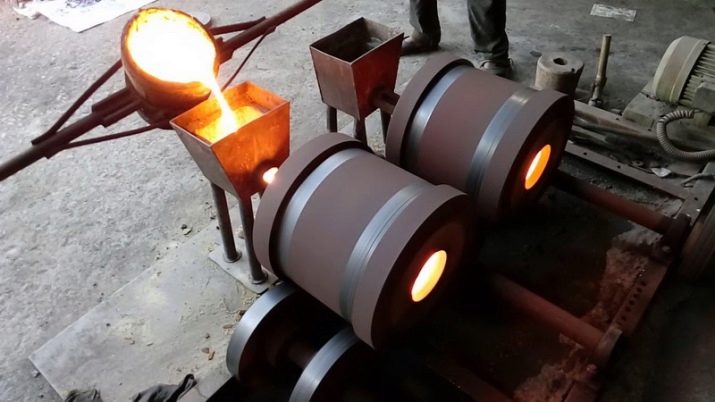
On machines with a vertical axis of rotation, the following is performed:
- propellers;
- worm wheels;
- gears.
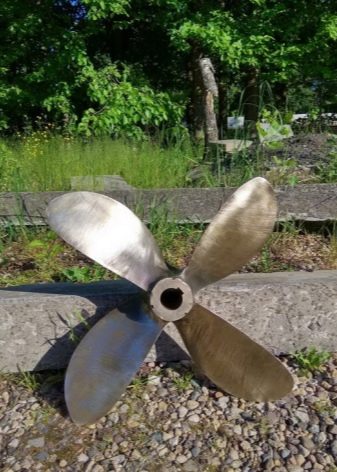
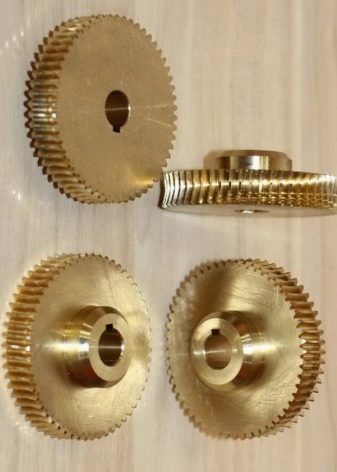
During the casting process, the sand is compacted and foreign elements are forced out.
Art casting
At home, use this method of making bronze. But this copper alloy has high fluidity, so it does not completely fill the mold, unlike the brass alloy. Because of this, the intended pattern on the surface of the part is blurred. To give clarity, minting is used. This is a rather laborious and time-consuming process. But at the same time, the most creative moment of artistic casting. The quality of the final product depends on the level of the embossing performed.
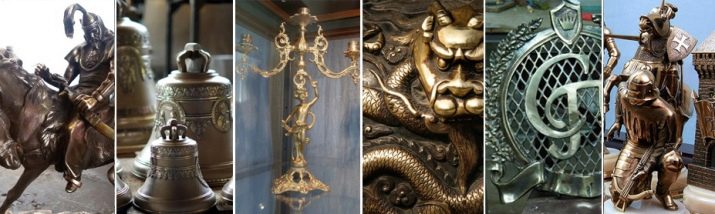
Stages of art casting:
- creation of a sketch and working drawing;
- production of a structure for creating a casting mold;
- production of a foundry model;
- preparation of the model;
- melting the charge;
- pouring molding mass into the casting model;
- cooling;
- extraction from the model;
- processing the finished product with a grinding machine, sometimes a metal brush is used.
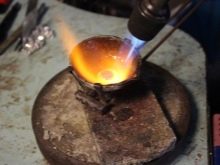
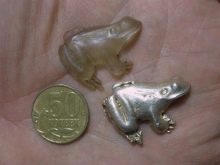
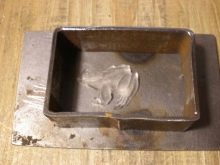
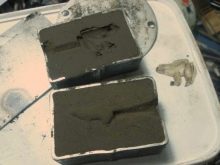
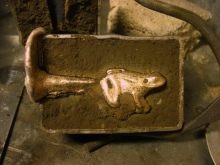
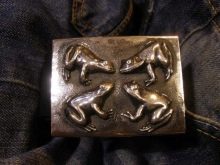
Finished individual components are combined into one product, if, according to the final design, it should be single, but consisting of several parts. Then the resulting finished figure is processed to remove minor imperfections, and covered with an upper protective layer.
Injection molding
This casting method is based on the effect of excess, vacuum pressure. The principle of a press is used, the melt is fed into the injection mold with excess pressure. The pneumatic or hydraulic system acts on the piston. Due to the high speed at which the high viscosity melt is supplied, an overpressure is created, the mold is completely filled.
Then, by vacuum suction, the molding mass flows into the cavity of the mold. It has thin walls surrounded by cold water. Cooling moves from the edges to the center. The melt is drawn in over a certain period of time. Then the pressure is normalized, and the excess residues of the molding mass flow down the walls.
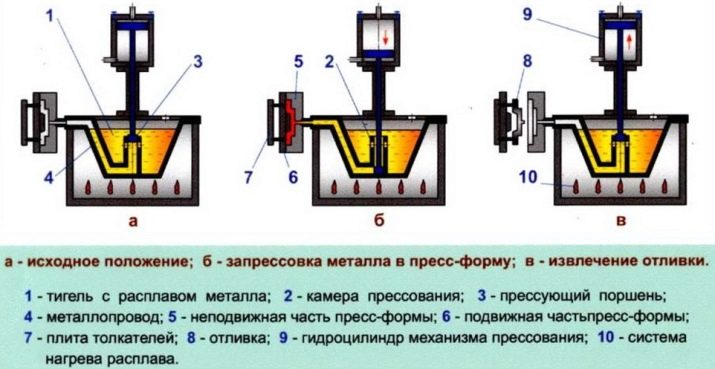
Due to shrinkage after cooling, the product can be easily removed from the mold. Due to automation, the mold is filled with melt in a fraction of a second, which significantly reduces the manufacturing time of parts and is an undoubted advantage of this casting method. Regardless of the casting method used, safety precautions must be followed in the manufacture of products from bronze and brass.
- When working, you need to use protective glassesto protect your eyes from droplets of molten material and fumes.
- Before starting an activity, you should put on gloves made of special heat-resistant material.
- The room must be well ventilated and ventilated, since during the melting of these alloys, gases harmful to humans are released.
- Shouldn't be allowed contact of flammable materials and liquids with heating devices.
- Necessary strictly follow the technology of the process. Since this production is quite traumatic.
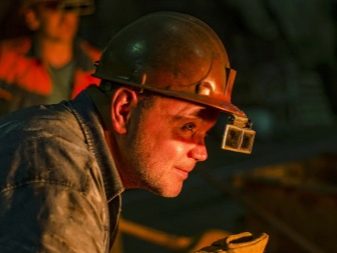
For information on how bronze sculptures are made, see the next video.