Temperature and methods of melting brass
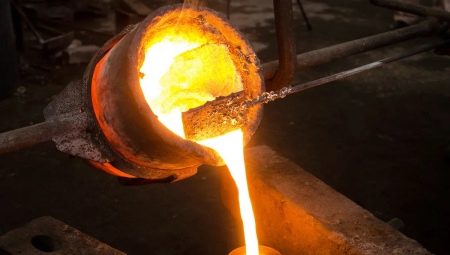
The temperature and methods of melting brass is a topic that deserves extensive scientific research, especially since the name of the alloy extends to various compositions based on copper. Brass can be two- or multicomponent, with the addition of nickel, lead and even tin, but according to the metallurgical classification it does not belong to bronzes. They undoubtedly have common signs, but the physical and chemical properties are determined by the constituent components.
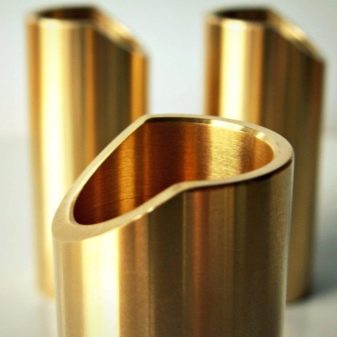
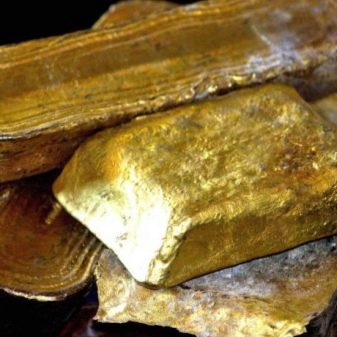
Melting point of brass
Specialty handbooks always indicate that the melting point depends on the composition, which can be variable.
Clean
What is brass? In fact, it is an alloy based on copper with the addition of zinc (sometimes tin).
The melting point of pure brass is 880-950 ° C.
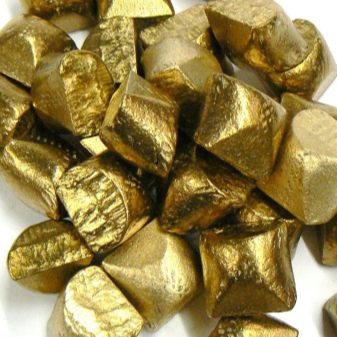
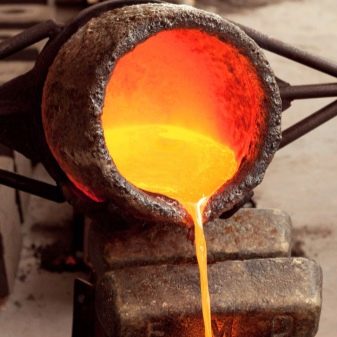
With impurities
The main determining factor is the amount of impurities and their percentage. The alloy has been known for a long time, so it has many variations. In addition to copper and zinc, there may be other chemical elements. On this basis, brass is divided into Alpha and Beta.
- Alpha - single-phase, with a zinc content of less than 40% melts at a temperature less than 905? (in degrees Celsius). This is due to the prevalence of copper, which melts in less hot conditions.
- Beta, two-phase, stronger, but not so plastic, in addition to two main ingredients, it can contain aluminum and silicon, nickel and manganese (not very typical additives) and more usual ones - tin, lead and iron, which provide the necessary strength and resistance in atmospheric conditions, during technical operation.
- Special, prepared for certain needs, are less common; in their manufacture, when determining the composition, the characteristics necessary for the part and product are taken into account. They are divided into extra hard, hard and soft or annealed alloys.
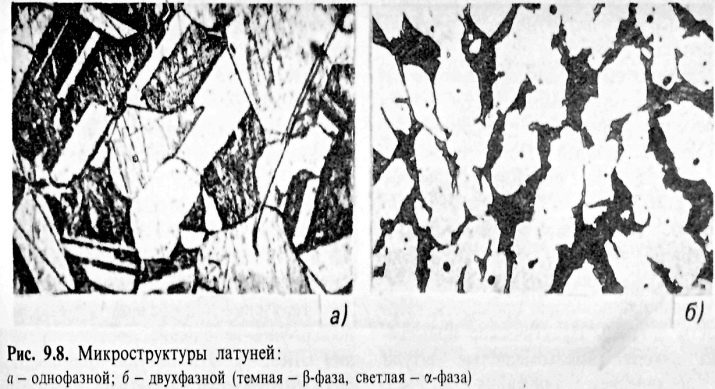
Foundries melt easily, because they contain up to 50% copper. But here, too, the melting point is determined precisely by its percentage, and it can vary from 30 to 50%.
Casting and even cutting with a laser are possible only at a correctly selected temperature, and this important indicator fluctuates in the collapse from 889 to 950 C, while the specific heat and melting point in this composition of metals do not coincide in any case, if we are talking about different grades of single-phase brass.
Two-component, or Beta-brass, differ from them by the coincidence of important characteristics, therefore the difference between all variations is 161? Celsius.
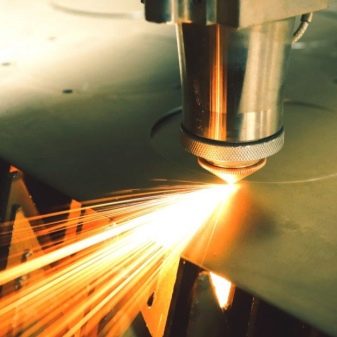
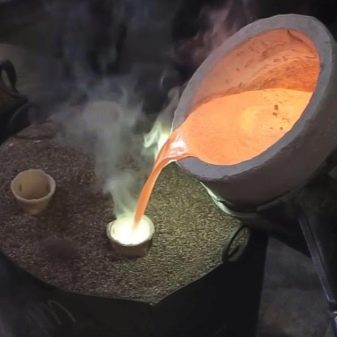
In reference books on metallurgy, the brand, composition and melting or casting temperature are always indicated. In two-component L-860, for example, it is 885-395 degrees, but in the LS59-18 brand, casting is carried out at temperatures from 1030 ° to 1080 °, while melting occurs at 900 °. When preparing for the process at home, it is imperative to take into account the composition of the metals that are included in the brass by its manufacturers. The more zinc it contains, the easier the heat treatment takes place. Broaching and rolling is possible if it contains more than 20% zinc, but if lead, bismuth or both are added, the process will be very difficult.
There are several options for determining the melting point of brass, but not all of them are acceptable in a home workshop. One can only make assumptions (when it comes to scrap brass), at the place or part where it was used by the manufacturers. There can be a huge number of needs in which a beautiful alloy that looks like gold in appearance is used, for example, technical details - pipes, bushings, separators and others.
For decorative purposes, it is used for tableware, souvenirs, finishing accessories (for example, door handles and curtain rods, frames, fasteners or functional parts in door and window systems). Often in the factory, a specialist works on the determination of chemical characteristics, especially when remelting diverse scrap
... It is he who establishes the processing modes that have long been defined and systematized in reference books by profession.
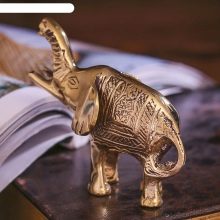
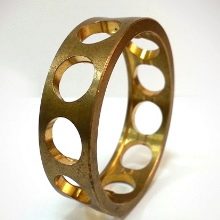
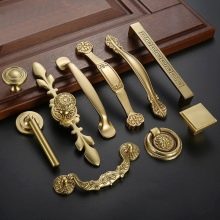
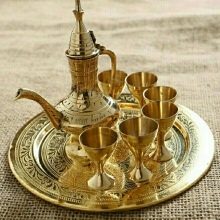
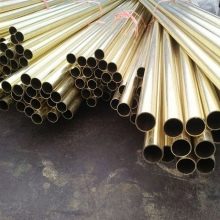
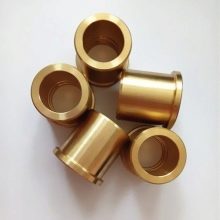
Methods for melting metal
In the conditions of an industrial enterprise, the process technology is determined by the brand and composition that must be obtained at the output. For this, the production has everything you need - special equipment, with well-thought-out fire safety measures, professionals who know the intricacies of the chemical process and their provision during work. Here you can vary the possibilities, obtaining the required melting temperature, automatically pour the molten mass into special containers and then use it for its intended purpose.
At home, this is not as easy as it seems to amateurs. Detailed instructions always mention that you need to have a home workshop, where annoying accidents such as fire or burns will be provided, the need to vary the temperature if it comes to an unidentified composition of scrap. And that's not counting the time spent and physical effort. However, craftsmen are rarely stopped by such trifles. They came up with several methods of melting.
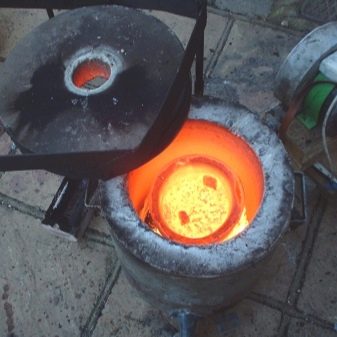
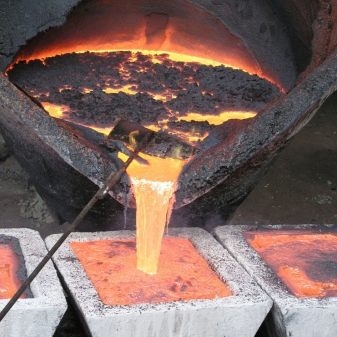
- Muffle furnace - the easiest way to handle brass alloys if available in workshop equipment. The home craftsman only needs to grind the scrap, place the crucible in it and select the appropriate melting point. However, not everyone who works on metal has such furnaces, since they are not cheap.
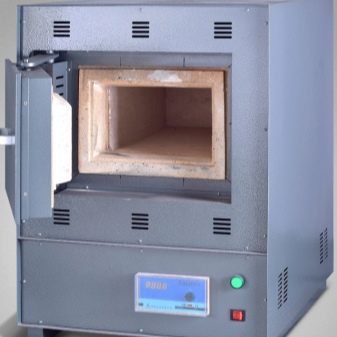
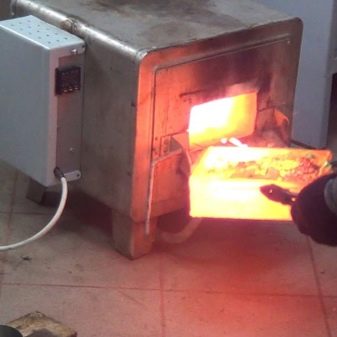
- Gas-burner - a more democratic in cost, and therefore, a more affordable tool for purchasing in your own needs. But even in this case, you have to do some preliminary steps - to securely fix it in an upright position and provide appropriate fire-fighting measures.
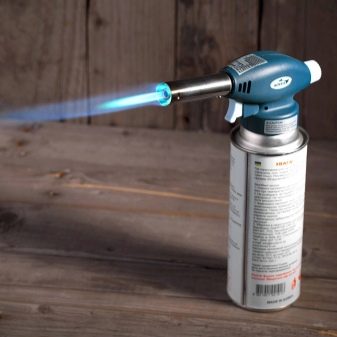
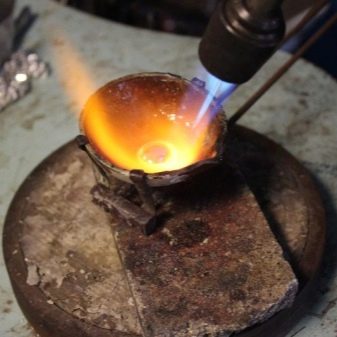
- Homemade oven from refractory bricks, in which you can use induction elements powered by electricity. Complete with it, you will have to make a crucible, reliable and heat-resistant, and the tongs with which they take it out of the furnace. Of course, all this must have increased strength. Although the latter two can be purchased at specialty stores, DIYers prefer their own melting tools, which use a variety of belay options.
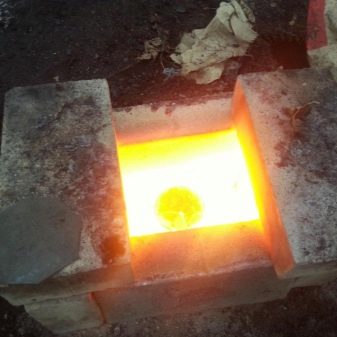
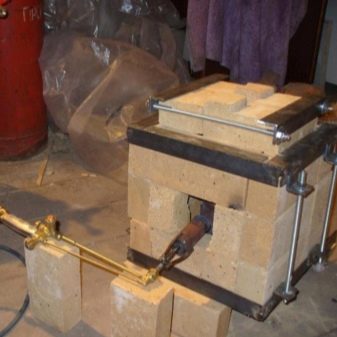
Each of the methods of processing alloy at home has its undeniable advantages. The optimal, safe option that does not require additional manipulations is a special oven in which the temperature reaches 1000 degrees. However, a significant drawback is the high cost, which is not affordable for everyone who works in a home workshop.
Self-made is more democratic, but building materials will be required for construction, external tightness, additional devices for the melting process. A gas burner is the cheapest method, but it also has its own significant drawbacks. To use it, you need to have a room in which all the necessary conditions are provided, protective equipment, tools for crushing scrap.
The smaller the pieces of brass, the faster the melting of the raw materials used begins.
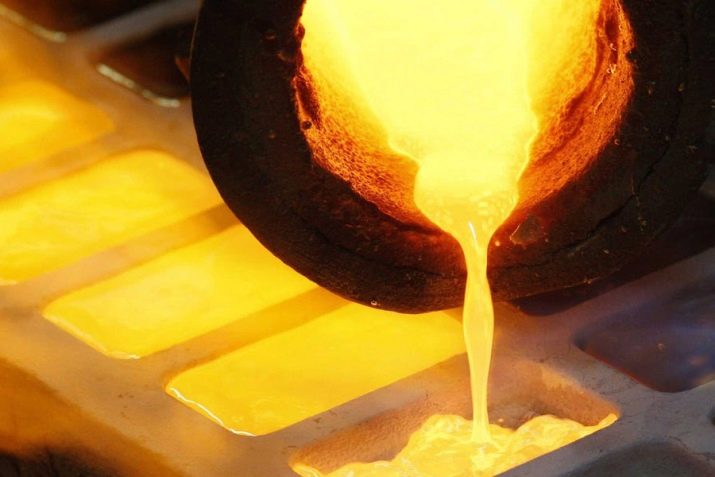
How to melt at home?
The answer to this question is contained in the equipment used. It is easy to work with a professional furnace - you need to set the required temperature with a thermostat and place the crucible inside. The advantage of such equipment is the high temperature, which will allow the home craftsman to work with other alloys, bronzes, and non-ferrous metals. A properly made home stove is also a good way out.
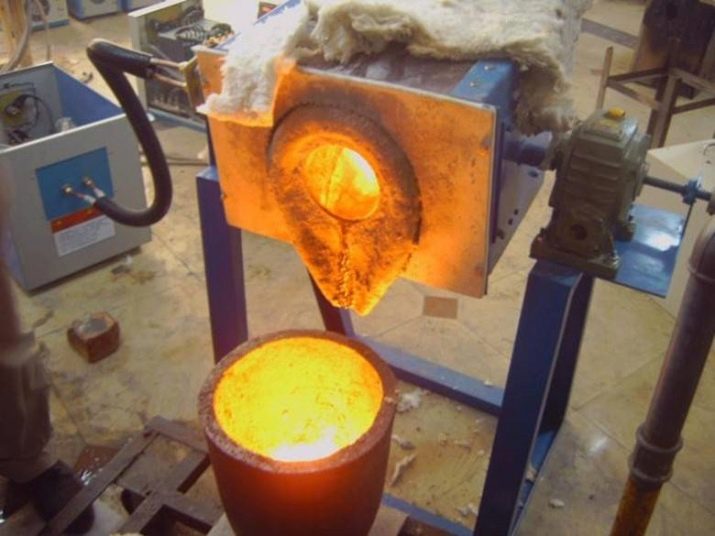
Preparation
The smelting furnace is laid out of refractory bricks (it is better to use grades with increased capacity). It must be securely fixed with a heat-resistant solution, and some craftsmen are taking measures to protect it from thermal effects - they are coated on the outside with special compounds. The recommended erection site should be well ventilated, but at the same time reliably sheltered from natural influences. Therefore, a sufficiently powerful ventilation is installed in the workshop, or it is placed in the courtyard under a canopy.
The heating element is ceramic induction tubes. The power of the energy source is at least 30 kW, with the highest possible efficiency, production is made only of high-quality parts. Additional accessories - a crucible, tongs with rounded edges and a long handle, a spoon for pouring molten metal is better to buy from the factory. However, some craftsmen prefer to make their own crucible from chamotte with an additional protective layer instead of a graphite container - this can be liquid glass with the addition of talc or a potassium silicate solution.
With intensive work with metal, the duration of any such device will be short.
Chamotte will withstand more melts than graphite, but you won't have to bother with a purchased one.
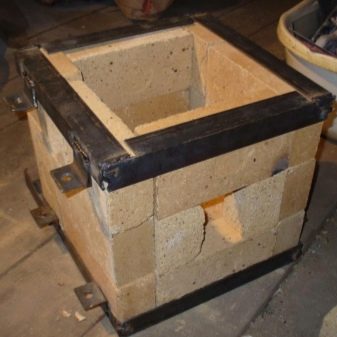
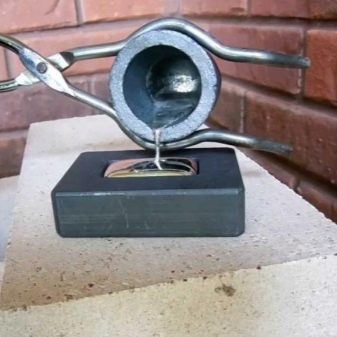
Process description
The scrap at the disposal of the master is placed in a melting container, pre-crushing. This will save both time and energy costs - the smaller the resulting fragments, the faster the result can be achieved. This is an important circumstance if you need to remelt a large amount of a metal alloy for some reason. Only after the container with the metal is placed in the oven does it begin to warm up. The crucible is removed with tongs, but before that you need to make sure that all the pieces placed in the furnace are completely melted.
A film may form on the surface of the metal (this depends on the scrap used); you need to prepare a handy tool for it in order to remove it immediately after removing it from the oven.
For casting, a pouring spoon and wooden molds are used, they do not have to be reused, because they will become unusable while the metal cools down.
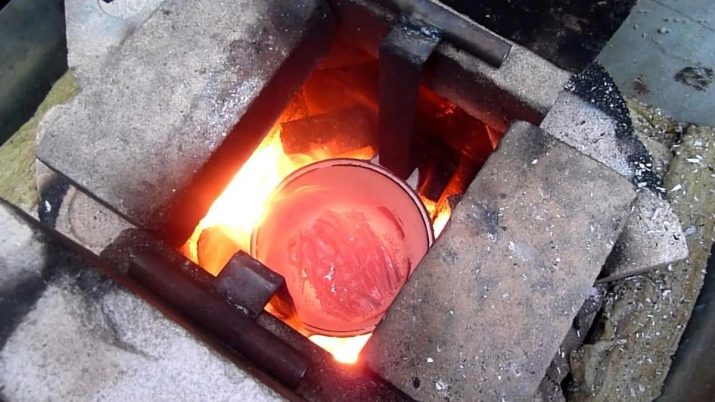
There is nothing complicated in the description, like in preparing a dish - they put it in the oven, get it, pour it into vessels, wait until it cools down. However, the first experiments may be unsuccessful due to some nuances - for example, insufficient heating due to a heating element, placement in an already heated oven, due to inexperience or if instructions are not followed. The part may not correspond to the required parameters and may need mechanical rework if the molds for casting are inaccurate. Therefore, now they are printed, if possible, on a 3D printer, using metal that exceeds brass in terms of heat resistance.

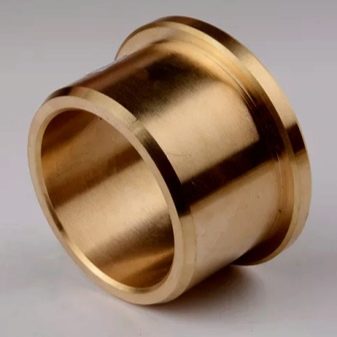
Safety engineering
The main danger that awaits a novice master is injury or burns. Therefore, work in a home workshop requires imperative adherence to safety precautions.
In any instruction, you can find 3 rules necessary for melting without consequences - ventilation, protective clothing, coating with heat-resistant properties on the floor or walls of the room.
- Clothing is chosen with long sleeves and trousers, certainly made of natural fabric, which is difficult to catch fire. Synthetic overalls are not an option, they melt quickly and can cause serious burns. Shoes - high, dense, for the face and eyes it is better to take protective glasses and a mask, for hands - work gloves.
- Heat-resistant materials are used to avoid a fire in the event of splashes of hot metal on the floor or walls. The easiest way out is an asbestos sheet.
- Ventilation is an indispensable element of indoor equipment. Toxic substances formed in the air when brass melts can lead to dangerous consequences - general poisoning of the body. If there is no money for it, the oven can be installed outdoors.
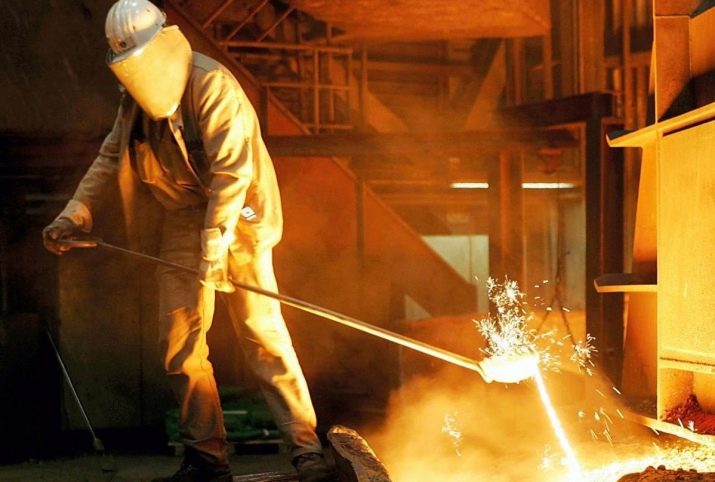
Brass is a grateful, beautiful and reliable alloy that has been used for many centuries. Smelting or refurbishing it is a great way to make decorative items, plumbing fittings, fasteners. The main thing in this creative process is adherence to instructions and safety precautions.
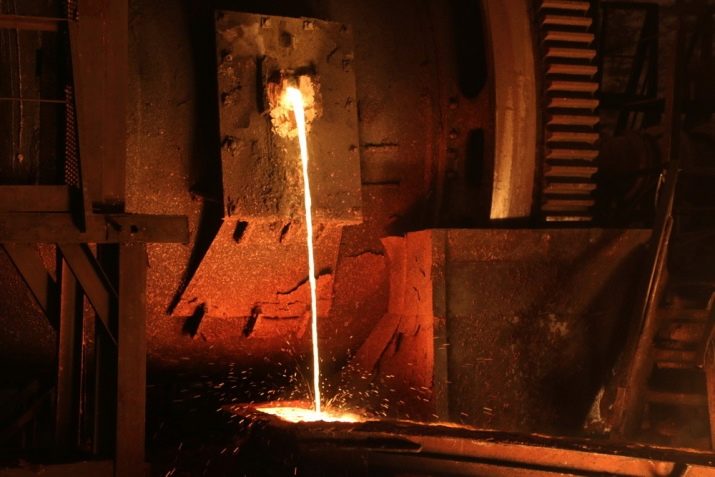
All about the temperature and methods of melting brass, see the next video.