DIY methods for making a kitchen knife
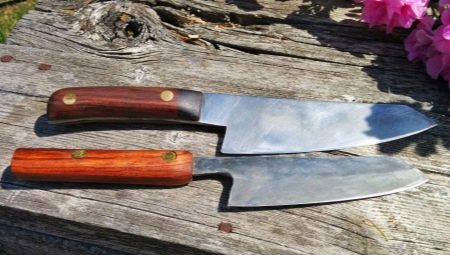
If you want to make a kitchen knife with your own hands, then this article was written especially for you. Making knives is a slow, delicate, painstaking, multifaceted, sometimes frustrating process. Such a business will require skills in metalworking, woodworking and design. It will take a lot of patience, attention and general level of preparation.
Model selection
First you need to draw a future fillet knife and circle the resulting shape on graph paper. Try to draw the knife to scale, that is, in real size. The fewer changes you need to make to the design, the better.
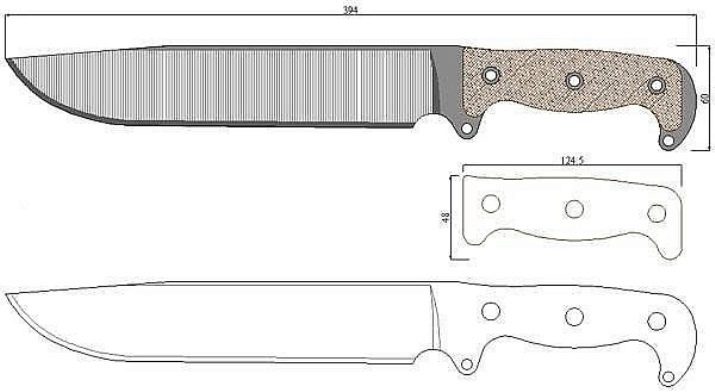
Now you need to decide how the handle will attach to the knife blade. There are three common ways to make a full, partial, or through knife.
The handle consists of two identical parts - for example, wooden parts. A partial way is when the blade of the knife extends into the shaft, which the handle then hides. The handle parts are placed on the rod and secured. By the way, this method is used to make Japanese swords and sushi knives.
A through knife is similar to a partial knife, but the extension of its blade extends through the entire handle so that the handle can be secured with a nut or thread at the other end. Most knives with typesetting handles are made this way.
Choose the model that you like best and get to work.



Selection of materials
Of course, it is best to use stainless steel to create the blade. In addition, it will be more convenient for beginners to make a knife from a quick cut (steel).So, you need a strip of metal between 30 and 60 cm in size.
In addition, you will need pen material such as wood, micarta, bone, leather, cord, stone, gem, ivory or meteorite... Of course, it is best to use a tree for the first time. Wood is a unique, beautiful and rather tough material. You will also need special rivets and epoxy to attach the handle. Or you can use a brass rod, making special pins from it for fastening.
After solving the issue with materials, you need to make a layout that will be identical in design to your drawing.

Cutting out a blade for a knife
To do this, you will need the following tool.
- Hacksaw for metal with multiple blades.
- Little Bulgarian.
- Drill with a set of drills.
- Files of various shapes.
- Vise.
- Necessary protection - special glasses, gloves, jacket.






The work algorithm consists of several points.
- Cut out the blank for the blade with a metal hacksaw or grinder. If you have a thick piece of steel, use a hard hacksaw. We recommend using standard blades. If you cut the blade from thin steel, then the process will not take long. You need to cut out a rectangle, inside which will be the main shape of the blade.
- Cut out the shape of a blade with a shank for the handle. This can be done with a grinder with a thin disc for metal.
- File the cuts with a vise. To avoid damaging the metal with teak sponges, use wooden blocks for clamping. If a belt sander is available, the sanding can be entrusted to it. The metal will change color during cutting and processing due to the thermal changes that take place in the steel. This will not affect the strength of the knife in any way.
- Sanding the edges. For this process, it is best to use a wheel with coarse sandpaper so that you can gently sand the slope down to the middle of the steel. Sand the other edge in the same way until it is even. In the process, you need to be patient and careful to avoid rough processing. Work the edges evenly to get an even and regular shape.
- We drill holes for rivets. Make sure you are using a drill that is the same diameter as the shaft or rivet that you plan to use to attach the handle to the blade. There can be any number of such rivets, so decide on the required number.
- We make a handle for a knife and attach it to the blade.




Blade formation
Before heat treating the blade, you need to finish it. This is necessary to get a quality product in the end. To complete the blade, you will need:
- sandpaper from 60 to 220 mm (you can use a grinding wheel and a drill);
- grinding block (even when using a grinding wheel);
- files.
This is the easiest step. You need to start grinding the blade with the finest sandpaper and go up to 220. The main thing is not to save money, because later you will regret the scratches that were not removed in time.
Always carry out each subsequent sanding perpendicular to the direction in which you worked previously.


Heat treatment
Heat treating the blade is perhaps the most technically difficult part of the entire process. You can use a coal forge or a gas forge to forge metal.
The next hardening step is to heat the knife to a lower temperature (about 400 degrees Celsius). Thanks to this, the knife will be less brittle and retain its relative strength.
Now you will need a tempering bath. Use oil for steel. Different types of steel require different quenching methods - oil quenching, water quenching, air quenching.
You must completely submerge the blade in water until it cools completely. The second thing you need to harden the metal is a magnet.It will help determine the hardening temperature, at which point the steel becomes non-magnetic.


Handle making
The sheet of paper on which your knife is depicted must be attached to a block of wood and outlined with a pencil. You only need to circle the handle, because we will cut it out in order to then attach it to the blade. Better to leave a few centimeters of indentation around the shape of the handle. You should have two of these mirrored parts of the handle, which you then attach to the blade on both sides.
Once you've got the shape of your future handle, use a band saw to cut out the shape of your handle.
Remember to leave at least 1 extra centimeter in place to avoid cutting too much material.
On the handle of the knife you need to do preliminary holesas stated above where you will insert your pins or rivets.
If your knife is riveted, you must sink the hole to the correct depth. You can use a vernier caliper to determine the size of the rivet head, which is the size of the hole to be drilled.
Before proceeding to epoxidize your blade and handle, Form and grind two identical handle elements.
Push the pins through the drilled holes to put the wood and metal in place. Now you can attach the knife with epoxy. Apply epoxy to one half of the handle and then join it to the blade and the other half of the handle. Once all the pieces are connected, take the two clamps and grip the knife handle. Let the product stand for at least 5 minutes.

Disc or disc brake knife
In the exact same way as described above, you can make homemade kitchen knives from a disc brake at home. It will also need to use a band saw, sander, belt sander and knife assembly tools.
Using a grinder or band saw, cut out the blade and shape it to the desired shape. Hot red-hot steel will have to be cooled, therefore you need to prepare a bath of water in advance.

See below for a video tutorial on how to make a DIY kitchen knife.