Features of openwork carving
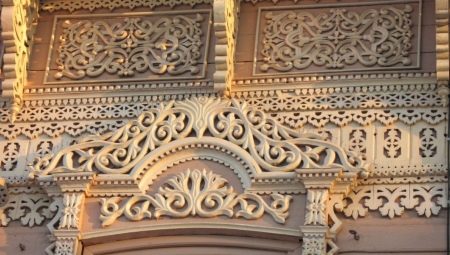
Weaving, embroidery, painting on fabric can be openwork, but it looks no less impressive openwork wood carving. It was believed that such patterns are able to protect the home from the evil eye: the evil spirit was entangled in a "curly" pattern, as if in a trap. Therefore, carvings appeared on children's toys, dishes, furniture, and spinning wheels.
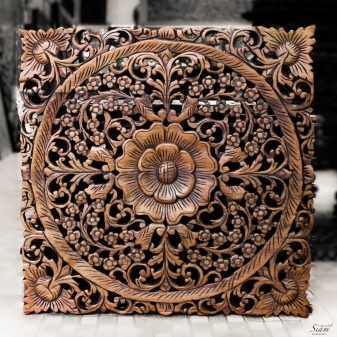
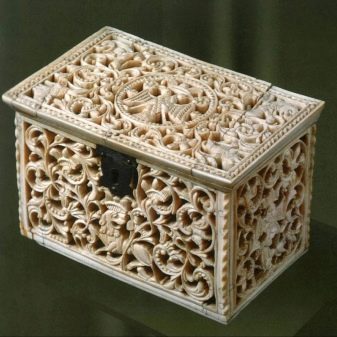
Features of technology
Cut openwork carving has a rich history. In Russia, its appearance is associated to a greater extent with the spread of Orthodoxy. In churches, openwork patterns adorned iconostases and altars, icon frames, icon cases (wall and floor).
The peak of creative thought was the royal gates, executed in the form of a Byzantine ligature, a vine with fruits. Openwork carving appeared, according to historians and culturologists, in Byzantium.
In everyday life, carving has reached great development in the Peter's era... It should be noted that the sovereign himself was a good carver, he also knew turning. This is my hobby he brought from Europe: there the tsar got carpentry tools, and already in Russia he ordered local craftsmen to make a lathe to make screw and openwork parts. Slit ship decor, furniture with openwork patterns were cleverly obtained in the hands of Peter.
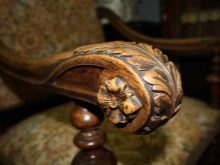
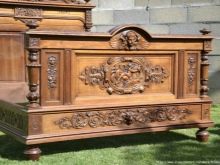
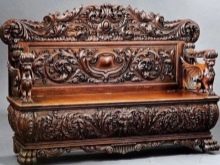
Interestingly, and Catherine the Great I was also fascinated by openwork carving, with pleasure I was engaged in this, not to say that it was a woman's business. Although one can argue with such a statement: at the St. Petersburg Institute of Noble Maidens there were courses of artistic carving... It was believed that girls engaged in this craft grow aesthetically, improve their artistic taste.
Basically, the cut openwork thread was used for the interior decoration of the dwelling.She also adorned the gables of houses, shutters and window frames, entrances.
Made with the help of carving and furniture, and dishes, as well as shelves, hangers, spinning wheels, brothers. In Soviet Russia, children were also engaged in it: in numerous circles of the houses of pioneers, children learned the ancient craft, and this was an honor.
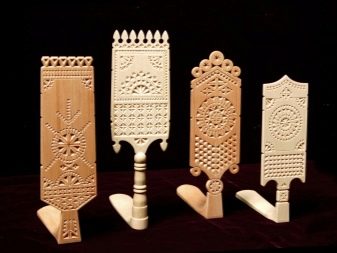
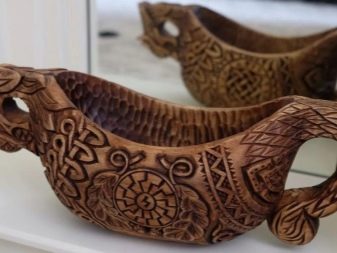
Today, openwork carving does not lose its significance - it becomes the same decoration of furniture, interiors, facades of houses... The customer still prefers to decorate his life with natural materials and traditional design.
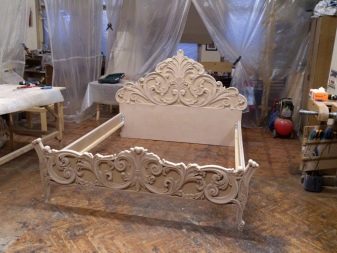
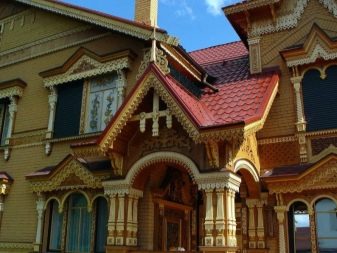
Where is it used?
First of all, these are large and small interior elements. For example, openwork wooden partitions do not lose their popularity (and, perhaps, are even gaining more and more popularity). A chic zoning element in the kitchen-living room can be in the form of a partition with beautiful slotted patterns.
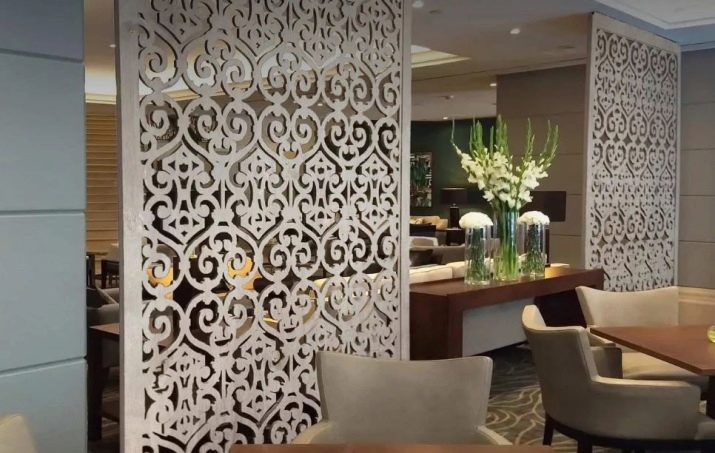
To decorate furniture carving is still used actively, and if not everyone in the house can imagine such a design, then for a summer residence you want something beautiful, subtle, causing nostalgic feelings. Wood carving allows you to make beautiful openwork crockery and cutlery. And working with simple plywood, you can make interesting shelves or hangers.
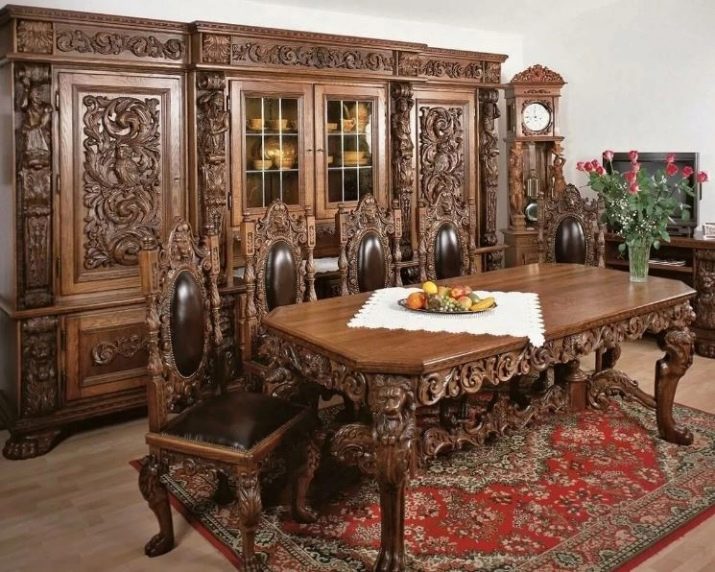
If the product is able to integrate into an already created interior, to become its harmonious part, then the openwork carving will be excellent home decor way... And since the interior trends of recent years sing a hymn to natural and simple materials, natural shades and textures, traditionalism in choosing a style of decoration, you can definitely bet on openwork techniques.
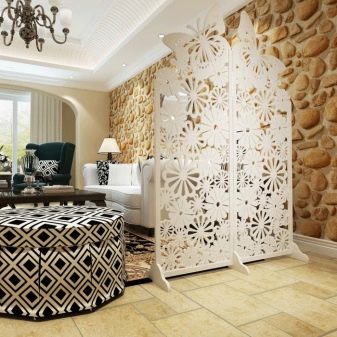
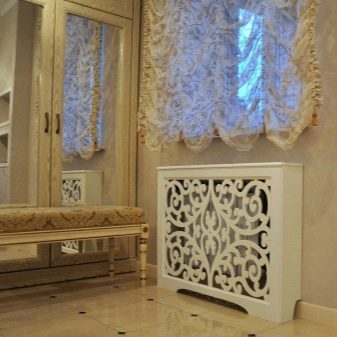
Comparison with other threads
Openwork carving is such an artistic way of processing wood, in which the background is completely removed.... The picture turns out, as the masters themselves say, “bottomless”. It is due to this that the product comes out light and airy, and because of this it acquires a special charm. Sometimes openwork thread is called through.
How does the end-to-end technology differ from the flat one: the latter has a background, a flat surface.
The pattern, thus, form various shapes and sizes of recesses and recesses. There are several types of such threads - geometric, contour and staple.
In addition, the pattern is removed to the background in the flat-relief thread, while in the flat-embossed thread it protrudes above the background. It is worth mentioning for comparison also the volumetric carving, which allows you to create three-dimensional wooden compositions. This is sculptural carving, a special kind of art. It does not imply any cuts and the absence of a background.
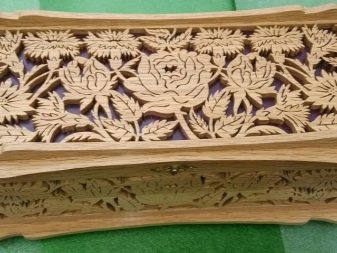
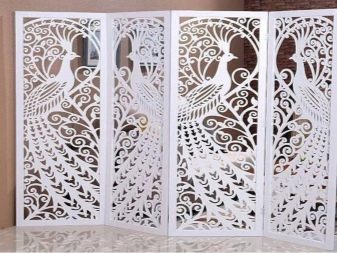
Pattern overview
Wooden lace is formed in two ways: sawn and cut. Each is interesting in its own way.
Sawing
Carpentry and joinery tools are used to create them; a cutting tool is also needed for finishing. The sawing thread is based on a planar through ornament. For example, the patterns of sawing strips, which are located on the house facades, look incredibly beautiful.
And against the background of the wall, floristic or geometric patterns of through curls and lines look luxurious.
In sawing carving, craftsmen are very fond of referring to the images of birds and animals. Women's silhouettes are also popular themes, the basis for future patterns. The most requested element is the S-shaped curl with curled ends.
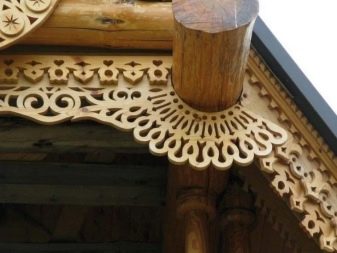
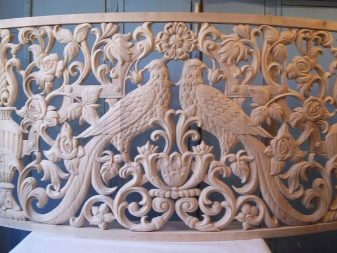
Slotted
Usually these patterns use flat ornament. Thread elements without a background are forced to touch each other and the frame. If the elements of the pattern are different in height, such a thread is called openwork. In the slotting technique, the remote areas of the background are not the most significant in size, but they are beautiful in shape. They form that attractive pattern that so distinguishes the openwork carving.
The main difference between slotted patterns and sawn cut patterns is the way to get the falling out parts. So, in the slotting technique, the mesh is made with a cutter, in the sawing technique - with a circular saw. The theme of the patterns is similar: there are many plant elements, there is an image of a person and an animal.And, of course, geometric patterns are also in demand.
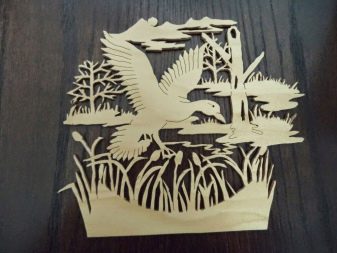
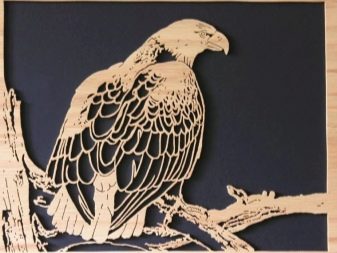
What tools are needed?
It is worth starting, nevertheless, with a description of the material. The tree must be of good quality, especially well dried. The material is taken only homogeneous, preferably - from one section of the tree, knots and rough texture stripes should also not be.
The basic set of tools includes:
- knives and chisels;
- needles;
- hacksaws for metal;
- sandpaper with different grain sizes;
- vice;
- drill with drill bit variations;
- bars;
- jigsaw.
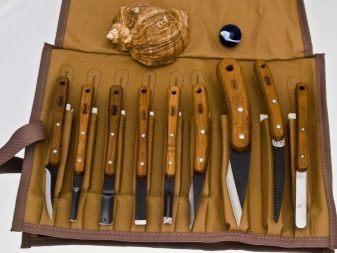
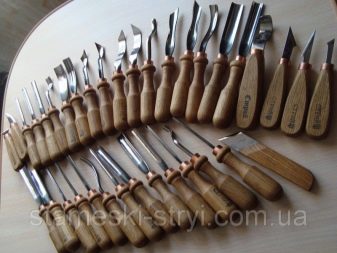
Knives must be made of high quality steel. These may not be the most expensive domestic models, they are not much inferior to imported ones. Instead of chisels for carving, sharpened screwdrivers or even a file. Chisel flat has a long shaft, at the end of which there is a cutting flat edge. It is convenient to use such a tool for primary processing of wood.
A semicircular chisel is the most important tool in carving, its variations differ in the degree of roundness.
It is worth mentioning that the carver's entire toolbox is divided into 2 types: manual and electric. Hand tools are relatively inexpensive and easy to operate. But manual labor does not have the highest productivity. Electric tools help to speed up and at the same time simplify the processing of wood. They are more expensive, but the quality of work with their use increases.
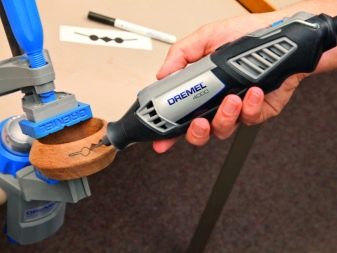
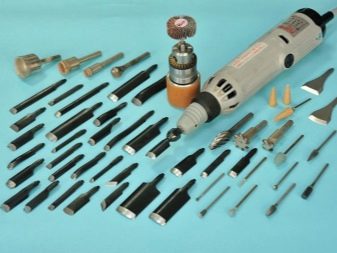
A few words about modern carving tools. Flexible shaft, for example, makes it possible to obtain a carved product of almost any complexity. And it is not so expensive, often beginners acquire this tool for themselves. Or take laser engraver - this is already a real multifunctional equipment, which has a stock of nozzles and different processing modes.
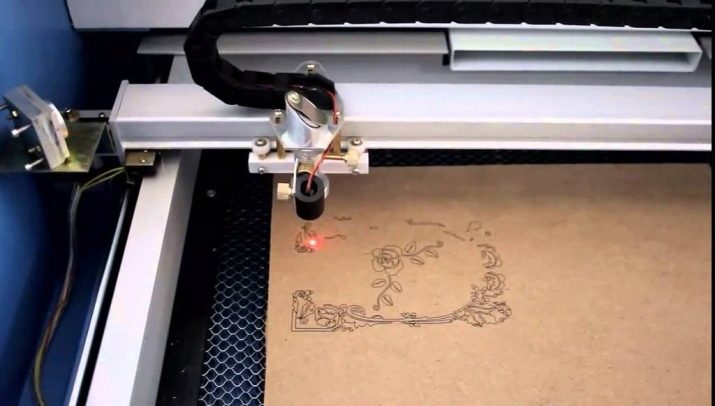
Execution technology
Openwork carving begins with a sketch of the future product.
Usually, first rough sketches are made on a small scale, after the project is approved, you need to make a sketch on paper in a 1: 1 scale with detailed detailing.
And to translate an ornament (or an ornamental plot composition) from paper to wood, you will need templates, carbon paper, pencil and tracing paper.
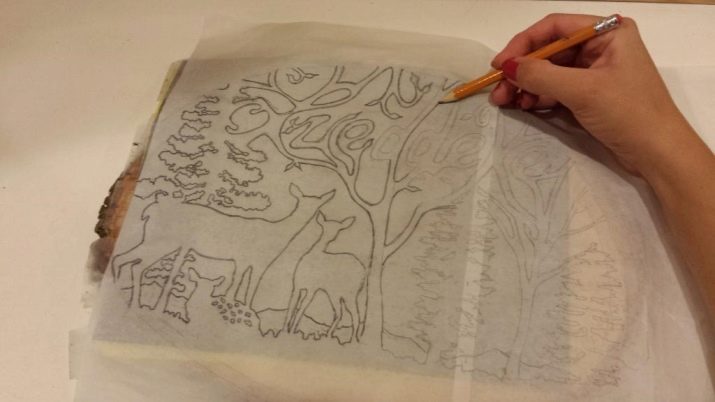
Let's consider an algorithm for making a product using the openwork carving technique.
- The prepared material (wood) will have to be sawed, planed and trimmed. This is done either by hand or at a power plant. Further, usually all workpieces are calibrated on a thicknessing machine (to maintain the exact thickness).
- The material needs to be cut and cleaned, adjusted according to a pre-prepared form, and then glued in segments. An ornament can be applied to the finished form.
- Before cutting out the background part, you should prepare the shape. That is, with a drill with the required diameter, the drill should make preparatory holes according to the already applied picture.
- Next comes the most interesting stage of the carving - the execution of the artistic processing of the slotted elements. It is always work with knives, chisels, and other tools convenient for the master. The stage for each carver goes on in its own way: someone cuts out the details for a long time, stretching the work for several days. Someone goes through this stage quickly. It depends both on experience and on whether the tools are familiar to the master.
- After the openwork artistic carving is completed, the master cleans up the work well. If necessary, he grinds it and glues the product.
- At the final stage, the finished product is well inspected so as not to miss defects and roughness. The wood can now be polished with a piece of wood or a coarse cloth. Completely finished work is treated with water-based stain or alcohol. One layer will not always be enough.
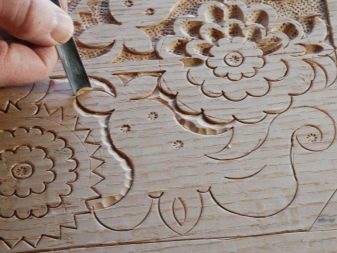
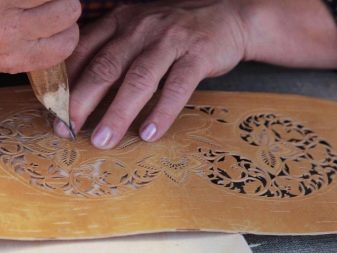
It remains only to wait until the product is completely dry. - it is ready and can take its place in the interior, on the facade or anywhere else.
Openwork carving - this is experience, and artistic inclinations, and creative search, and the ability to see the work even before it is ready. One thing is clear for sure - the ancient craft today finds a new meaning and meets the needs of a modern customer.But the technique and material remain the same. And such a union of tradition, quality and a new look gives rise to beautiful openwork things.
How to make a wood box with cut openwork carving, see the video.